The Scientific Research Behind Porosity: A Comprehensive Overview for Welders and Fabricators
Comprehending the intricate mechanisms behind porosity in welding is essential for welders and fabricators aiming for impressive workmanship. From the composition of the base materials to the intricacies of the welding process itself, a wide variety of variables conspire to either aggravate or relieve the existence of porosity.
Understanding Porosity in Welding
FIRST SENTENCE:
Assessment of porosity in welding reveals important understandings right into the honesty and quality of the weld joint. Porosity, defined by the visibility of cavities or spaces within the weld steel, is a common issue in welding processes. These spaces, if not effectively dealt with, can endanger the structural integrity and mechanical properties of the weld, resulting in potential failures in the finished product.
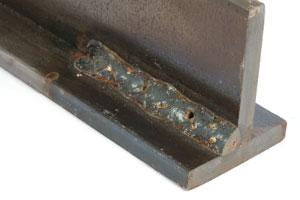
To spot and evaluate porosity, non-destructive screening approaches such as ultrasonic testing or X-ray assessment are typically employed. These strategies enable for the recognition of interior defects without compromising the honesty of the weld. By analyzing the dimension, shape, and circulation of porosity within a weld, welders can make informed decisions to enhance their welding processes and accomplish sounder weld joints.
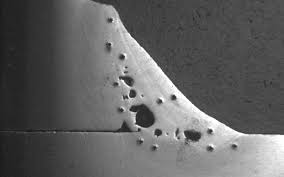
Aspects Affecting Porosity Development
The incident of porosity in welding is affected by a myriad of factors, varying from gas shielding efficiency to the ins and outs of welding specification setups. Welding parameters, including voltage, present, take a trip speed, and electrode type, additionally influence porosity formation. The welding strategy utilized, such as gas steel arc welding (GMAW) or protected metal arc welding (SMAW), can affect porosity development due to variants in heat circulation and gas insurance coverage - What is Porosity.
Effects of Porosity on Weld High Quality
The existence of porosity likewise weakens the weld's resistance to deterioration, as the caught air or gases within the gaps can react with the surrounding atmosphere, leading to degradation over time. Additionally, porosity can hinder the weld's ability to withstand pressure or influence, further jeopardizing the total high quality and dependability of the bonded framework. In vital applications such as aerospace, vehicle, or architectural building and constructions, where security and toughness are paramount, the damaging impacts of porosity on weld top quality can have extreme consequences, emphasizing the special info significance of reducing porosity with appropriate welding techniques and treatments.
Strategies to Minimize Porosity
Furthermore, using the suitable welding criteria, such as the appropriate voltage, current, and travel rate, is important in preventing porosity. Preserving a consistent arc size and angle during welding also assists minimize the chance of porosity.

Utilizing the proper welding technique, such as back-stepping or utilizing a weaving motion, can also help distribute heat uniformly and lower the opportunities of porosity formation. By carrying out these techniques, welders can efficiently minimize porosity and produce top quality bonded joints.

Advanced Solutions for Porosity Control
Carrying out advanced technologies and ingenious approaches plays a critical duty in accomplishing superior control over porosity in welding procedures. Furthermore, utilizing innovative welding methods such as pulsed MIG welding or modified environment welding can also aid alleviate porosity issues.
One more advanced remedy entails the use of advanced welding tools. As an example, using tools with integrated functions like waveform control and advanced power resources can improve weld quality and minimize porosity dangers. In addition, the application of automated welding systems with precise control over criteria can substantially reduce porosity flaws.
Additionally, incorporating innovative next surveillance and examination modern technologies such as real-time X-ray imaging or automated ultrasonic testing can help in identifying porosity early in the welding procedure, permitting immediate corrective activities. Generally, integrating these advanced solutions can substantially boost porosity control and improve the overall top quality of bonded parts.
Final Thought
Finally, comprehending the science behind porosity in welding is crucial for welders and fabricators to generate high-grade welds. By determining more the factors influencing porosity development and carrying out strategies to reduce it, welders can boost the overall weld high quality. Advanced options for porosity control can additionally boost the welding process and make sure a strong and reliable weld. It is essential for welders to continuously enlighten themselves on porosity and implement best practices to accomplish optimum results.